Energy Efficient Fan with EC Drives | How do VSDs & EC Fan Compare | EC Fan & Motor FAQs
- SEA Energy
- Jan 24, 2021
- 7 min read
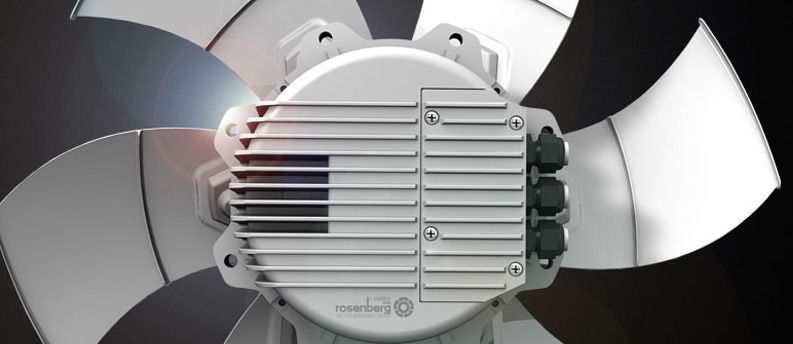
Table of Content
Overview of Electrically Commutated - EC Fan technology
EC Stands for Electrically Commutated, where AC and DC voltages are combined to provide the best of elements of both technologies. The motor runs on a DC voltage, but with a normal AC supply. EC fans are capable of intelligent speed control – further reducing energy consumption.
EC electric motors utilize a permanent magnet in the secondary field. When the rotor is energized it creates a repelling magnet, thus allowing the motor to rotate within the field. 30% less energy is saved in EC over an AC motor, as the secondary magnet field does not need to induce energy to create a magnetic field.
Fans that move air and pressurize the data center’s raised floor are significant components of cooling system energy use. After mechanical cooling, fans are the next largest energy consumer on computer room air condition (CRAC) units.
One way many data center managers reduce energy usage and control their costs is by investing in variable speed fan technology. Such improvements can save fan energy consumption by as much as 76 percent.
With the different options on the market, it may not be clear which technology is best. Today, variable speed drives (VSDs) also referred to as variable frequency drives or VFDs and electrically commutated (EC) fans are two of the most effective fan improvement technologies available.
The advantages of both options are outlined below to help data center managers determine which fan technology is best for achieving energy efficiency goals.
How do EC fan technologies work?
Variable speed fan technologies save energy by enabling cooling systems to adjust fan speed to meet the changing demand, which allows them to operate more efficiently.
While cooling units are typically sized for peak demand, peak demand conditions are rare in most applications. VSDs and EC fans more effectively match airflow output with load requirements, adjusting speeds based on changing needs. This prevents over-cooling and generates significant energy savings.
With VSDs, drives are added to the fixed speed motors that propel the centrifugal fans traditionally used in precision cooling units. The drives enable fan speed to be adjusted based on operating conditions, reducing fan speed and power draw as load decreases. Energy consumption changes dramatically as fan speed is decreased or increased due to the fan laws. For this reason, a 20 percent reduction in fan speed provides nearly 50 percent savings in fan power consumption.
EC fans are direct drive fans that are integrated into the cooling unit by replacing the centrifugal fans and motor assemblies. They are inherently more efficient than traditional centrifugal fans because of their unique design, which uses a brush-less EC motor in a backward curved motorized impeller.
EC fans achieve speed control by varying the DC voltage delivered to the fan. Independent testing of EC fan energy consumption versus VSDs found that EC fans mounted inside the cooling unit created an 18 percent savings. With new units, EC fans can be located under the floor, further increasing the savings.
How do VSDs and EC fans compare?
Energy Savings One of the main differences between VSDs and EC fans is that VSDs save energy when the fan speed can be operated below full speed. VSDs do not reduce energy consumption when the airflow demands require the fans to operate at or near peak load. Conversely, EC fans typically require less energy even when the same quantity of air is flowing.
This allows them to still save energy when the cooling unit is at full load. EC fans also distribute air more evenly under the floor, resulting in more balanced air distribution. Another benefit of direct-drive EC fans is the elimination of belt losses seen with centrifugal blowers. Ultimately, EC fans are the more efficient fan technology.
Cooling Unit Type VSDs are particularly well-suited for larger systems with ducted upflow cooling units that require higher static pressures, while EC fans are better suited for downflow units.
Maintenance In terms of maintenance, EC fans offer an advantage. EC fans also reduce maintenance because they have no fan belts that wear and their integrated motors virtually eliminate fan dust.
Installation Both VSDs and EC fans can be installed on existing cooling units or specified in new units. When installing on existing units, factory-grade installation is a must.
Payback In many cases, the choice between VSDs and EC fans comes down to payback. If rapid payback is a priority, then VSDs are likely the better choice. These devices can offer payback in fewer than 10 months when operated at 75 percent. However, EC fans will deliver greater, long-term energy savings and a better return on investment (ROI). While EC fans can cost up to 50 percent more than VSDs, they generate greater energy savings and reduce overall maintenance costs, ultimately resulting in the lowest total cost of ownership.
Have the experts weigh in Service professionals can be an asset in helping choose the best fan technology for a data center. Service professionals can calculate the ROI from both options, and they can recommend the best fan technologies for specific equipment.
Service professionals trained in optimizing precision cooling system performance can also ensure factory-grade installations, complete set point adjustment to meet room requirements, and properly maintain equipment, helping businesses achieve maximum cooling unit efficiency today and in the future.
Whether you ultimately decide to go with VSDs or EC fans, either way, you’ll be rewarded with a greener data center, more efficient cooling, and significant energy savings that translate into a better bottom line.
EC Fans fitted in Air Handling Unit_AHUs
Air Handling Units are fitted with the latest fan technology which delivers increased efficiency as a result of consuming far less power than a standard AC motor.
With the different options on the market, it may not be clear which technology is best. Today, variable speed drives (VSDs) also referred to as variable frequency drives (VFDs) and electrically commutated (EC) fans are two of the most effective fan improvement technologies available.
The advantages of both options are outlined below to help data center managers determine which fan technology is best for achieving energy efficiency goals.
EC Fan Features and Benefits
High Efficiency – compact motor controller solution cooling effect by air stream around the motor/controller is optimum
Future proof and ready for ERP.
Reduced energy consumption. On average 30% less electricity than conventional fans
Significant noise reductions within the motor due to switching frequencies of built-in inverter drive
No need for additional motor protection. EC fans have their own motor protection for over-current and motor temperature
Easily integrated with BMS control
Easy to maintain, maximum service life
Speed consistent operation over whole voltage bandwidth
Space saving design due to external rotor motor concept
Maximum speed independent of main power/frequency
Integrated status LED – no separate display or other tool for status failure diagnostic
High flexibility through different add-on modules – easy extension adaption possible
Speed controller or PID closed loop function by AM Premium module for application refrigeration, air volume, differential pressure control, temperature control, air velocity and more – no external PID control unit necessary
We provide Industrial Energy Efficient Equipment's
SEA energy offer a wide variety of EC fans and motors from top manufacturers, as well as offering a wide range of EC fan replacements for all types of ventilation, covering Axial, forward curve and plug fans etc. Also we are offering below mention energy efficient products:-
Premium Efficiency Fans for HAVC Systems (EC + Fan)
Energy Efficient Motors (IE-3,IE-4, IE-5)
Energy Efficient Pumping System
BLDC Celling Fans , Efficient Lighting Automation Systems
Water Saving Plumbing Accessories (Water Saving Nozzles, Washing Guns, Orifices etc.)
You have any requirements for the EC fan and motor or industrial Energy Efficient equipment's/technologies, then you can contact us via contact us form or email us to sea@seaenergy.in
EC Fan & Motor - FAQ
Q: What are electronically commutated motors?
Ans: Electronically Commutated motors are brush-less DC motors where the direction of the electric current is switched using electronic controllers. As the switching of the current is technically known as 'commutating', brush-less motors are also called 'electronically commutated' motors. EC motors provide the advantages of brushed DC motors in terms of the ability to have variable speed control, but without the drawbacks of brushes.
Q: What are the advantages of EC motors?
Ans: EC motors are very high efficiency electric motors (80%) and maintain a high efficiency level at part speed. This means that in most cases they use less than one third to half of the electricity used by traditional induction motors, which in turn translates into lower operating costs and short payback periods. As EC motors have a higher efficiency this ensures that the motors run cooler in application which ensures a longer life for the motor.
In terms of speed control and features, because the motor’s operation is controlled by software, EC motors allow customers to optimize and integrate the motor, fan and controller with the application, and to include features like data communications, constant volume control, variable speed.
Q: What about cost?
Ans:The initial outlay for an EC motor is more expensive than the traditional induction / shaded pole motors and this is mainly due to the electronic components required to drive the commutation. In recent years the cost of electronic components has reduced dramatically as volumes increase. The huge energy savings provided by EC motors, mean equally large savings in operating costs, which in turn translate in payback periods as short as a few months combined with a longer life expectancy. In our case, together with high energy savings, low use of raw material, low part count and simple electronics, have allowed us to make our motor price very competitive.
Q: How are EC motors 'sustainable'?
Ans: The huge energy savings provided by our EC motors directly translate into large carbon emissions savings. By using an EC motors in your application we are able to assist our customers in dramatically reducing the air pollution (CO2) generated by their applications. This is due to the motors high efficiency & low energy costs which helps to preserve the world for a ‘greener’ future. EC Motors are designed & manufactured using 70% less copper and 80% less steel than traditional induction and shaded pole motors which has a dramatic reduction in environmental impact in producing these raw material components.
Comments